在過去的十年里針對零間隙堿性電解的研究表明,透過“Zero Gap”設計的電解池性能可以實現顯著提高。通過采用更緊湊的電池設計,這可以為堿性電解的性能提供一個階梯式提升變化的潛力,如下圖所示,傳統設計與零間隙設計的主要區別在于使用多孔電極而不是金屬板(還有一個區別在于極板流場也在發生變化)。這使得電池具有非常小的電極間隙,緊湊的設計和很高效率。它迫使氣泡從電極的背面釋放出來,減少了它們對電池電解電壓的增加(減少了氣液混合相里面大氣泡導致電阻增加導致電耗增加)。
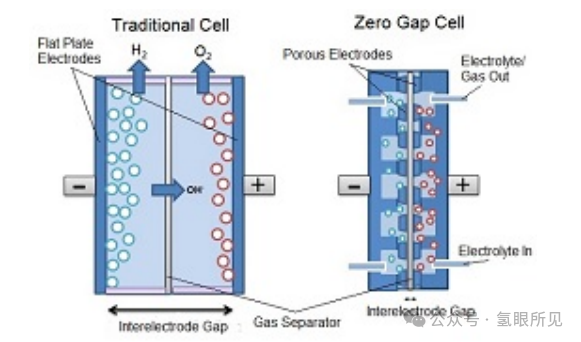
零間隙堿性電解
零間隙堿性電解是通過壓縮氫氧離子傳輸膜或氣體分離器(隔膜)兩側的兩個多孔電極來工作的。這使得兩個電極之間的間隙等于膜的厚度(<0.5 mm),而不是傳統設置的(> 2mm),從而顯著降低了兩個電極之間由大量電解質產生的歐姆電阻。氣體擴散層提供從多孔電極到雙極板的電氣連接,同時允許電解溶液的進料補給,并去除氣體產物(請仔細琢磨這里的結構)。
1967年,Costa和Grimes首次提出了零間隙堿性電解,在微孔氣體分離器(隔膜)兩側使用網狀電極(基本上目前多數已經做到了這一點)。當代的重要研究表明,零間隙設計的電解池電流密度可以大幅增加。最近的研究主要集中零間隙結構在陰離子交換膜電解槽上的開發,它具有低阻值和在差壓下操作的潛力。包括使用高比表面積的泡沫電極等新的電池設計也被開發出來了,以及采用直接沉積在(隔/分離)膜上的類似燃料電池類型的膜電極(MEA)方式。與傳統方法相比,零間隙設計更為復雜,因此結構部件也有所不同。零間隙電解槽采用多孔電極壓在蝕刻或沖壓的流場板(雙極板)上,而不是采用于有限間隙電解的單一平板類。催化劑材料要么直接沉積在多孔電極上(現狀較常用),要么直接沉積在膜上(AEM技術盡可能采用該方式),而傳統的設計是將催化劑直接沉積在平面極板上(這已經是一種很古老的做法了)。現狀用的電催化材料都可以直接轉移到新的設計中,只是沉積(涂覆)方法可能需要調整以將材料沉積到多孔基板上。兩種電池設計都可以使用相同的氣體分離器(隔膜),但是零間隙設計開辟了與陰離子交換膜一起工作的可能性(結構趨同性)。
基于鎳網/泡沫鎳的多孔電極已經在許多堿性電解系統中使用。另涂層不銹鋼在陰極方面使用也是一種可能性,盡管不銹鋼在氧氣存在的情況下受到高電位影響會發生氧化腐蝕。碳布(碳氈)已經被用于堿性燃料電池(陰極側),由于在高電位下易被氧化,所以它不適合用于陽極側。
雙極板必須具有良好的導電性、低接觸電阻和耐腐蝕性。鈦由于成本較低通常用于PEM電池,基于不銹鋼和鎳的板材是堿性電解槽的最佳選擇。石墨板可用于堿性燃料電池(AFC)的雙極板,但在陽極側經歷的高電位使石墨類材料不適合堿性電解的這一側。對固體聚合物燃料電池(PEMFC)的界面電阻分析,對使用材料進行了比較,表明隨著時間的推移,電阻的增加是由于在極板表面形成了不溶性氧化層。雖然電催化和氣體分離器(隔膜)材料的特殊特性對于指導個別領域的適當發展很重要,但它們在完整工作單元中的應用對于證明它們在更大規模上的可行性更重要。
膜電極組裝
零間隙設計的組件中心部分稱為膜電極組件(MEA),包括與膜兩側接觸的兩個多孔電極。有不同的方法來生產MEA,可分為兩大類:催化劑涂層附著在底物基體上(CCS)和催化劑涂層附著在膜上(CCM)。
這兩種方法都采用多孔電極,這提供了增加活性表面積的額外好處,因此對于相同的材料和電池設計,可以實現更高的電流密度。電池的性能取決于催化劑和膜的選擇以及電池設計,這使得不同電池設計之間的比較難以量化。零間隙電池的面電阻(Ω·cm2)包括膜電阻,以及電池各層之間的任何界面接觸電阻,該值允許在類似的零間隙電池之間進行一定程度的比較,并且有助于指導電池設計在整體電池性能中的重要性。
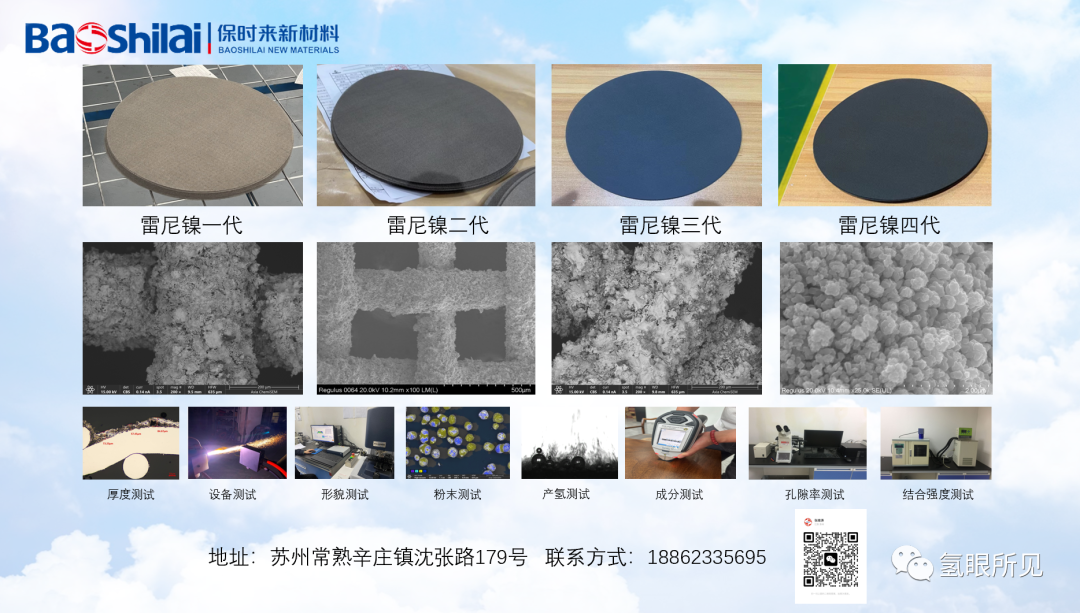
原文始發于微信公眾號(氫眼所見):“zero Gap”(零間隙)堿性電解槽的設計
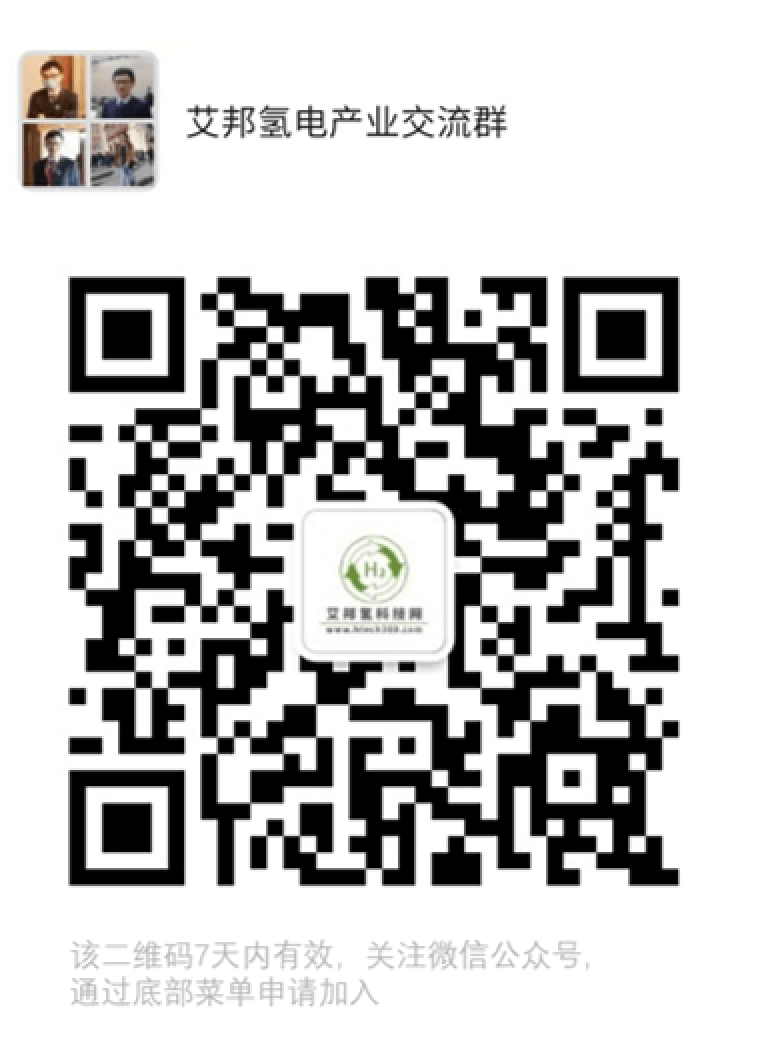