8月19日,在武漢經開區民營科技工業園,武漢理工氫電科技有限公司一派忙碌。恒溫潔凈生產車間內,國內首條自動化膜電極生產線開足馬力,一張張薄如報紙的黑色薄膜來回穿梭、組裝。
"這是我們自主研發生產的CCM型膜電極,已在國內1000多輛主流氫燃料電池商用車上實現批量應用,并出口至美國、德國、韓國等10多個國家和地區,實現了國產膜電極對國際壟斷的反向輸出。"武漢理工氫電總經理田明星說。
16年磨一劍實現膜電極國產化 膜電極是電堆里氫能轉化為電能的反應場所,它由催化層、質子交換膜、氣體擴散層及密封結構組成,被譽為燃料電池的"芯片"。
▲質子交換膜。
"一個電堆大概有3、400片膜電極,不僅成本占到電堆的60%以上,其性能更直接決定了氫燃料電池的應用表現。" 田明星說。
長期以來,由于新型膜電極量產制備技術被美國、日本等相關企業壟斷,我國在這一領域幾乎全部依賴進口,價格昂貴且供貨周期長,成為制約燃料電池商業化的"卡脖子"難題。
武漢理工氫電打破了這一局面。作為我國最早從事膜電極研發生產的企業,早在2006年,武漢理工氫電就致力于燃料電池零部件——膜電極(MEA)的技術自主化和大規模產業化。與武漢理工大學潘牧教授團隊合作完成的"低鉑、高效燃料電池膜電極組件制備技術及應用"項目,獲得湖北省技術發明獎一等獎,并在武漢經開區進入規模化產業應用。
▲武漢理工氫電的膜電極自動化生產線。
田明星介紹,與傳統膜電極相比,武漢理工氫電的CCM型膜電極,電流密度、功率密度均大幅提升,膜電極使用壽命增加到18000小時,貴金屬鉑的用量反而從每平方厘米0.8毫克降至每平方厘米0.4毫克,"這大大降低了燃料電池電堆的生產成本,為我國氫能產業發展提供了有力支撐。"
與此同時,在國家科技支撐計劃項目的支持下,武漢理工氫電還自主開發了國內首條膜電極自動化生產線,將膜電極從最初的單片生產升級到自動化生產,年產能提高5倍以上。2019年6月,基于該成果的產線建成投產,累計銷量突破200萬片,產品占據國內自主燃料電池市場主要份額。
"特別是北京冬奧會上,數百輛搭載北京億華通燃料電池系統的氫能大巴成功上路,圓滿完成各項保障任務,其中作為燃料電池系統核心部件的膜電極,就來自武漢理工氫電。"田明星說。
目前,武漢理工氫電已成為全球第5大膜電極生產商。自主開發的CCM膜電極,2007年獲得美國燃料電池備用電源公司的認證,成功打入美國市場,為沃爾瑪、亞馬遜等大型倉儲基地裝備了數萬臺燃料電池物流叉車。此后,又相繼拓展到德國、法國、韓國等多個國家和地區,充分展示了國產膜電極的競爭力。
明年膜電極產能將擴大5至6倍 除了在車用膜電極領域保持領跑外,近年來,武漢理工氫電不斷拓展產品范圍,自主研發面向制氫領域的PEM電解水膜電極。
▲技術人員正在膜電極自動化生產線上進行操作。
田明星告訴湖北日報全媒記者,作為未來國家能源戰略的重要組成,氫能產業遠不只有"用"氫的環節,上游"制"氫也同樣重要。根據預測,實現2060年碳中和目標,我國氫氣的年需求量將達到1.3億噸,其中可再生能源制氫(綠氫)規模有望達到1億噸。
"這為可再生能源PEM電解水制氫設備發展帶來契機,而膜電極,正是PEM電解水制氫設備中的重要部件。"田明星說,目前,國內PEM電解水制氫的膜電極還多為進口,價格昂貴、成本較高,影響了PEM電解水制氫技術的大范圍應用。
為實現國產化替代,2016年,武漢理工氫電率先啟動研發。自主開發的全新一代PEM電解水膜電極,具有高性能、高耐久性、高可靠性和強環境適應性、抗反極、低溫冷啟動等優點,目前已開始小批量生產。除了向國內多家PEM電解水制氫設備企業供貨外,還出口至歐洲市場。
憑借深厚技術積累,站上氫能"風口"的武漢理工氫電正迎來快速發展。"未來兩個月的訂單已全部排滿,今年上半年銷售收入同比增長了90%。"
武漢理工氫電還正抓緊打造國內領先的燃料電池零部件產業基地。投資2億元的新基地將于年內啟動建設,明年年底正式投產。新基地占地約30畝,將上馬兩條自動化膜電極產線,既可生產車用膜電極,也能生產電解水膜電極。達產后,年產能將擴大5-6倍,產品可同時滿足1至2萬輛氫燃料電池汽車的需求,全面助力我省千億氫能產業集群建設。
來源: 武漢開發區
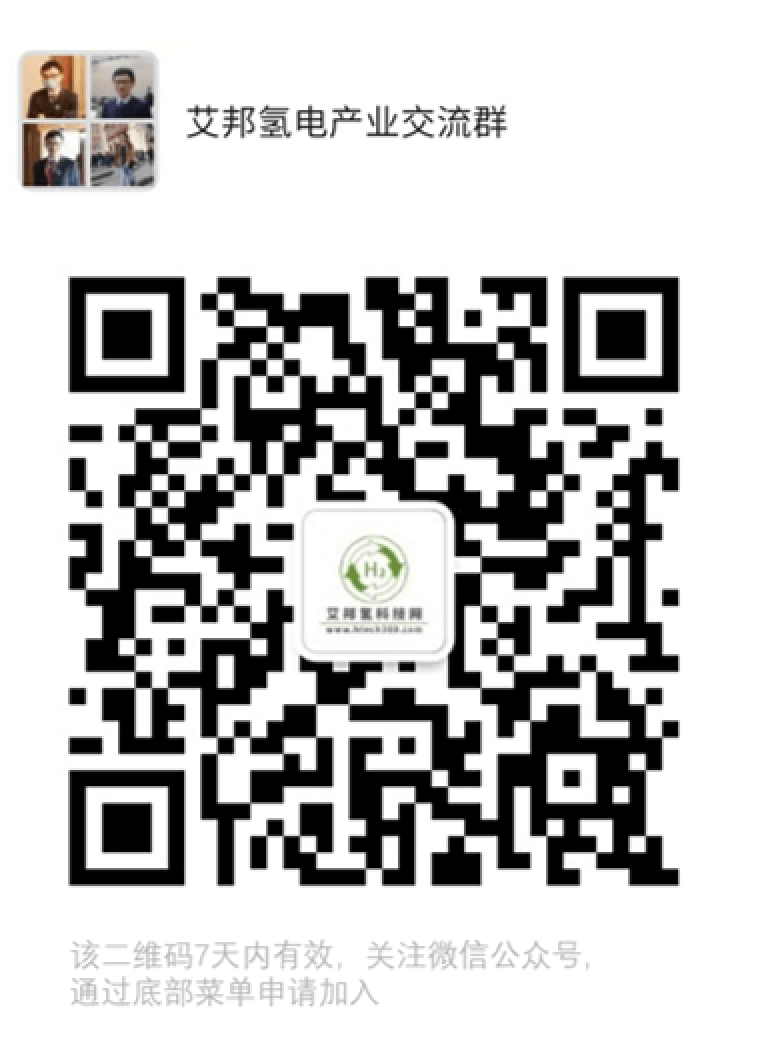